3D Printing: The Changing Art of Making Parts

Since acquiring Netfabb in 2015, Autodesk has been busy adding advanced technologies—including enhanced simulation, optimization and advanced toolpath capabilities—that will provide engineers and designers with a broad collection of additive design and manufacturing tools. Image courtesy of Autodesk.
Latest News
December 1, 2016
3D printing has come a long way from its early days as a prototyping tool. While that was big news in the early 1980s, additive manufacturing (AM) is increasingly being viewed as a viable on-demand manufacturing process, one that promises to revolutionize not only the way parts are made, but what materials are used to make them. Researchers are exploring how they can manipulate the structure and composition of the materials used at the particle level to ultimately affect and control performance characteristics of the finished part.

“Additive manufacturing creates new opportunities in many different areas, including remote fabrication for support and maintenance; rapid prototyping for realizing new concepts and experiences; but, perhaps most importantly, developing designs that were heretofore impossible to fabricate,” noted Dominique Florack, Senior Executive Vice President, Research & Development, Dassault Systèmes in a company press announcement.
By pairing AM with automated generative design capabilities, it is possible to create organic shapes that would be difficult for a human designer to envision, and impractical or impossible to produce with traditional manufacturing techniques.
In just a few months, we can expect to see the results of a partnership forged between Autodesk Research and Lawrence Livermore National Laboratories (LLNL) last year to develop a proof-of-concept protective helmet design that reflects how generative design software can be used to accelerate innovation of advanced material 3D printing. As part of an 18-month, in-kind cooperative research and development agreement, Autodesk Research gave LLNL access to its software for goal-oriented design as it studied how micro-architected metamaterials (materials with properties that don’t exist in nature) can be combined with additive fabrication techniques to produce objects that were not before possible. This type of research could eventually lead to breakthroughs in other areas of anatomically fitted equipment, such as body armor and prosthetics, suggests the company.
High Performance Parts from Engineered Materials
Today’s new AM-engineered parts may be lighter, yet stronger; and may be comprised of an array of innovative new materials—from carbon fiber or industrial-grade/medical grade specialty metals and resins to biomaterials and specially-blended multi-material plastic polymers that are digitally delivered “voxel by voxel.” They may take advantage of functional materials (e.g. materials that are thermo-insulating, or thermo-conducting) capable of enabling active smart sensors, or possess other unique electronic or mechanical characteristics such as the ability to print a battery within a 3D printed component.For example, a team from Virginia Tech’s Design, Research, and Education for Additive Manufacturing Systems (DREAMS) Lab was awarded first place for the inaugural America Makes for Innovation Sprint award for its 3D-printed “smart wing.” The theme for the competition was smart structures, which America Makes defined as parts with integrated devices, such as sensors, that were created via AM technology. The DREAMS Lab “smart wing” integrated sensing and actuation features to enable aircraft to autonomously adapt to flying conditions.
“Our goal was to use additive manufacturing to directly fabricate mechatronic devices—products that can both move, and have on-board sensing to detect and control that movement,” Chris Williams, associate professor of mechanical engineering and DREAMS Lab director told the Virginia Tech news service. “To demonstrate our progress toward this goal, we 3D printed a multimaterial wing with a control surface—that is the flap of the wing—that is both adjusted and controlled by embedded actuators and sensors.”
Processing Technology Makes Industrial 3D Printing Possible
During the past few years, equipment makers have been working on perfecting the technology that makes this kind of advanced industrial-strength 3D printing possible. Examples are emerging for all levels of production across the industry.
The start-up company, RIZE recently unveiled its RIZE One “office-safe” 3D polymer printer that features an Augmented Polymer Deposition (APD) industrial 3D printing process that the company says can print a proprietary compound of medical-and engineering-grade thermoplastics that can be manipulated at the voxel level, making it possible to change the material properties (e.g. strength, surface finish, geometric accuracy, and color) of the thermoplastic.
The ExOne Innovent 3D printer offers a binder jetting process that supports the ability to create functional parts, requires no support structures, and is designed to enable machine customization for customer-specific material requirements.
3D Systems’ Figure 4 3D printer introduces a modular stereolithography 3D printing system that offers printing speed improvements along with the ability to integrate with secondary processes (e.g. finishing and coating), and in-line 3D part inspection to ensure part compliance.
NVLabs has developed a high-speed, Metal Additive Deposition (MAD) multi-metal printing process that uses ordinary wire rather than powders to reportedly lower material costs by over 90%.
MarkForged’s Mark Two 3D printer is capable of printing continuous strand carbon fiber, Kevlar and fiberglass.
HP’s MJF (Multi-Jet Fusion) platform is designed to blend different inks to control material at the voxel level in order to vary stiffness, texture, color and more.
The new M 400-4 from EOS uses four lasers to improve direct metal laser sintering (DMLS) productivity.
Desktop Metal’s multi-metal desktop 3D printer, currently in development, promises to provide “an effortless way to go from 3D CAD to robust metal parts,” which the company says will make metal printing faster, safer and more affordable.
“End-to-End” Design through Additive Manufacturing
Whether you’re printing metal or plastic—the big news these days is that the era of industrial 3D printing has arrived, which supports a digital thread from concept design to prototyping to tooling and production-quality parts.
In a recent announcement, Siemens indicated that it is seeking to revolutionize product development with its end-to-end manufacturing solution—by integrating the entire additive manufacturing process from automated performance-driven design optimization to advanced 3D printing; and by supporting the use of “smart models” from design through simulation and final AM production, with no data conversion required. The portfolio will include NX, Teamcenter, Simcenter to help drive the design process, the company explains.
Dassault Systèmes’ 3DEXPERIENCE platform is intended to deliver an end-to-end solution including all engineering parameters using additive manufacturing. That includes material science, functional specification, generative design, 3D printing optimization, production and certification, according to the company.
Traditional 3D printer companies like 3D Systems have adopted this approach as well, recently announcing a comprehensive strategy to “evolve 3D printing from prototyping to production.” One way 3D Systems is seeking to accomplish this is through their new partnership with PTC, which involves working together to integrate 3D Systems’ 3D Sprint software development toolkit into PTC Creo.
Autodesk, too, has embraced this vision—recently announcing upgrades to its NetFabb 2017 tool for integrating design enhancement, manufacturing preparation and build simulation tools in a single environment.

Managing Materials Information In addition, companies like Granta Design and Materialise are aiding manufacturers with tools for both materials information management, and guides for using new materials in AM that incorporate years of experience working with—and documenting the performance of—a multitude of materials under a variety of conditions. Perhaps most importantly, the materials information management capabilities provided by these companies enable the traceability needed in the event of a part failure or a product recall.
GRANTA MI: Additive Manufacturing software, for example, was developed to bridge the materials information management requirements connected with AM-driven R&D, part design, simulation and production. According to the company, it enables users to build an additive manufacturing knowledge base that can help reduce R&D costs and support qualification and certification of parts. Data is captured in one place, with full traceability, using customizable templates.

In a similar fashion, Materialise offers a database management tool, Streamics where all process-related data (STL file revisions, part positioning, materials, powder batches, etc.) can be stored. Users can also store machine parameters and log files together with this data. Maintaining records of AM data in this way allows users to trace back part information, optimize processes and create reports in an efficient way.
More Info
Subscribe to our FREE magazine,
FREE email newsletters or both!Latest News
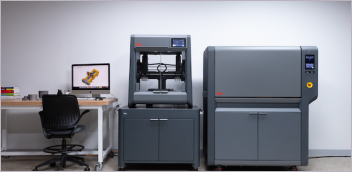
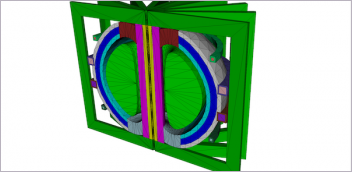
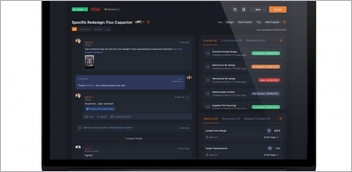
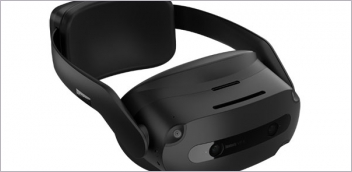